Here is a sequence of pictures taken while I was test-building these coach kits. I thought you might like to see this to see what is involved. The build went very well – it took an evening or two per coach, and was very enjoyable. You can judge for yourself how well the results have turned out.
Experienced builders will not need much of what is here, but I recommend that you have a glance through anyway as there are one or two aspects to the design of these particular kits you will want to know about.
I have shown the construction of the Third class and the Brake Third coaches. The First class coach is constructionally identical to the Third class coach, just with four compartments along the sides rather than five.
As you can see I have soldered the kits together, which is my preferred method, but there is no reason why they could not be glued, I suppose.
I use 60:40 Lead Tin solder (not Lead free solder – I find it impossible to get this to flow properly.) and Phosphoric acid flux which I buy from London Road Models or Model Signal Engineering, which I apply with a kebab skewer.
The etches as provided:


The body kits as built:
Brake third coach. D501.
Five compartment Third class coach. D401.
Two of the coach bodies. The First class coach is constructionally identical.
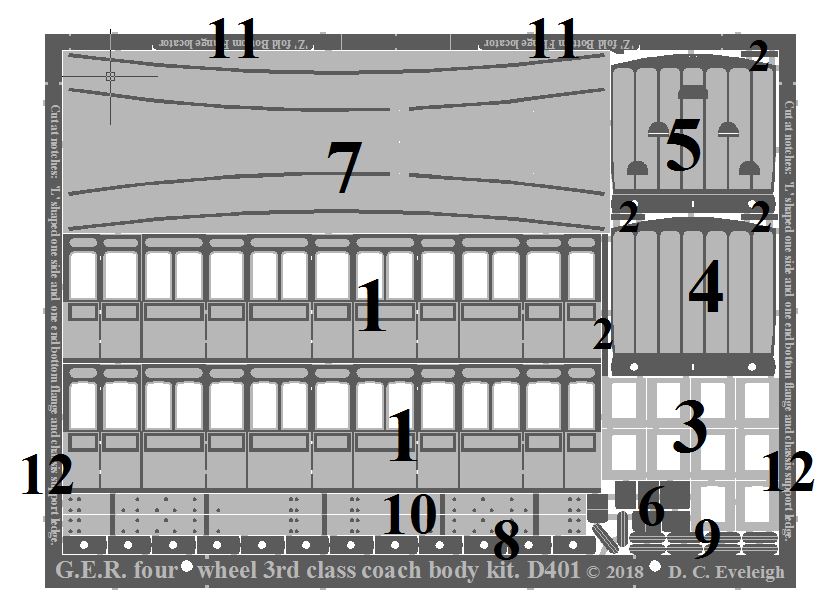
Parts identification
- Sides
- Strips for door hinges
- Drop-lights
- Plain end
- End with footsteps
- Footsteps
- Roof
- Head-stock thickeners
- Ventilators
- Sole-bar overlays
- ‘Z’ fold jig for supporting and locating bottom flange inside coach body whilst fixing in place.
- These parts of the etch surround form the bottom flange.
Cutting parts from the etch.
It is best to remove parts only when they are needed. I use a sharp chisel, cutting as closely to the part as possible, using a scrap of acrylic (perspex) to cut against. I prefer to use a brightly coloured piece of this as, one time, I was using clear perspex and hadn’t realised the tab I was cutting was beyond the edge, causing me to damage the etch. I have two chisels – the darker handled one I have had for years and it is probably one of the few antique tools I own. I mislaid it one time and so made the second from a knife edged needle file which I had regrettably, but conveniently as it turned out, broken some time earlier. I found it lost its edge quickly so had a go at heat treating it, which seemed to work. It is mounted in a graver handle from a tool supplier at an exhibition.
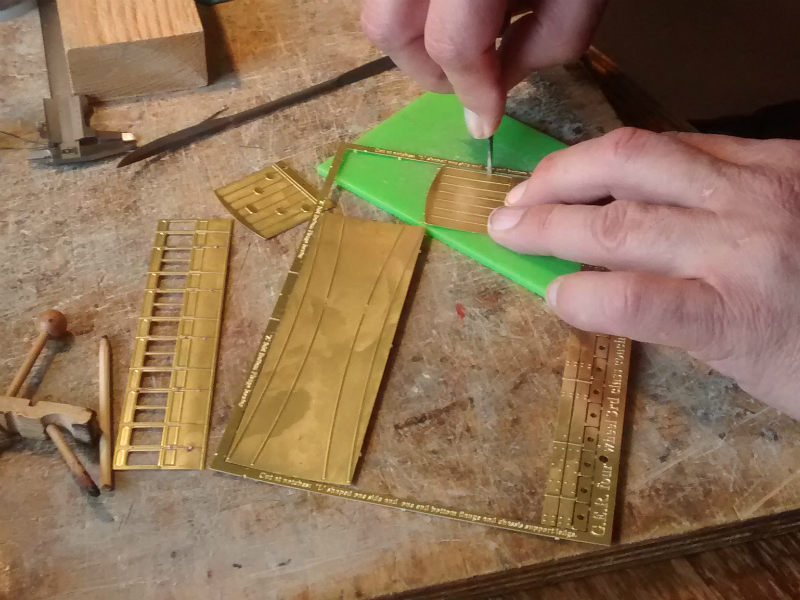
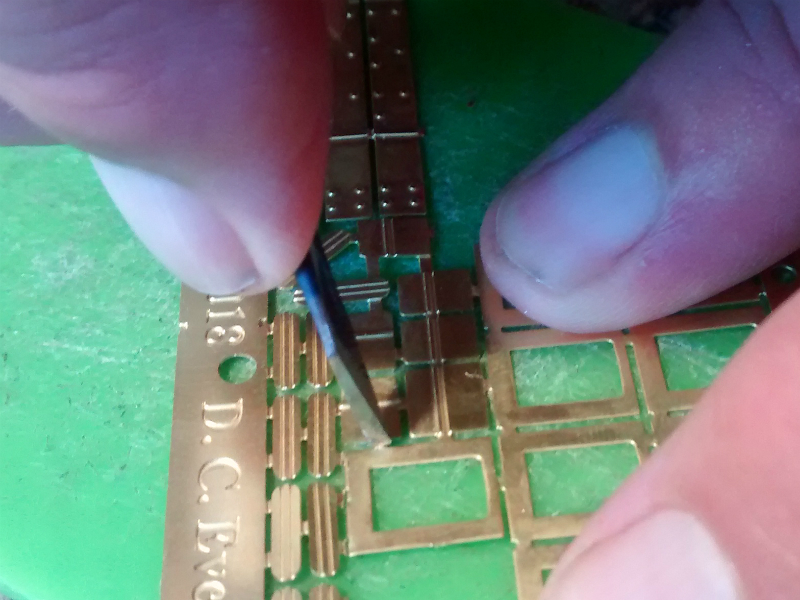

Cleaning the edge of etched parts.
It is usually necessary to clean up the edges of etches, partly because of the cusps from the etching process and partly to remove the evidence of the tabs. Depending on the size of the part I use a file of suitable length, usually managing to hand hold the part and guide the file against a finger as shown in the photos. Some people prefer to use sharpening stones or emery paper glued to blocks.
The mug of tea is pretty much mandatory, I think.
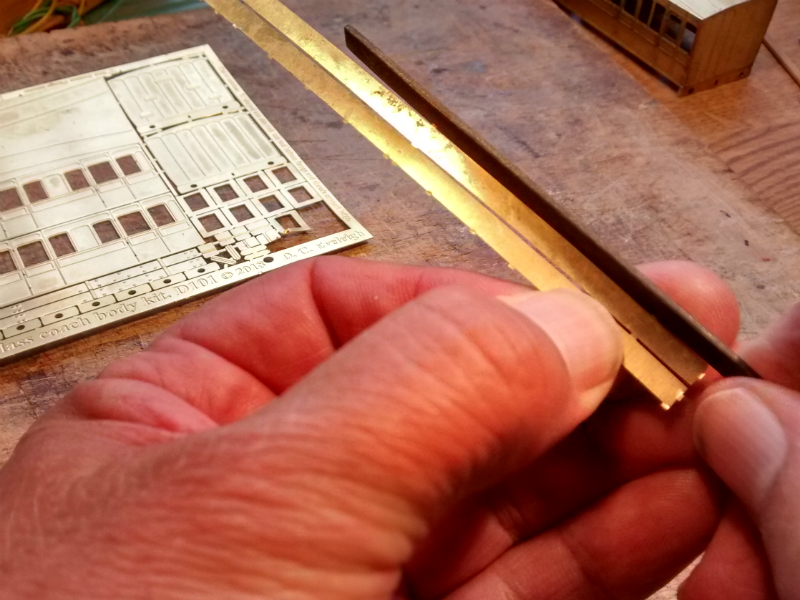
Rolling the ‘turn-under’.
People often refer to this as a ‘tumblehome’, but I am informed that this is incorrect. Tumblehome is apparently a naval term referring to an inward curve towards the top of a ship’s hull, and thus inappropriate for the inward curve towards the bottom of a railway vehicle. It is a really easy job to do anyway – mouse-mat, length of brass bar – press firmly and roll backwards and forwards until the desired curvature is achieved. If you overdo it, turn it face up and gently persuade it with the roller from on top.
Orion Jig
I use this for all my assembly work. It is a fairly basic device which I developed over a number of years building etched kits in 2 mm scale. I do actually sell these here, if you do not want to make one for yourself.
The name comes from the pattern of holes it amused me to provide for mounting the clamps. The first one I made I drilled far too many holes and kept losing small parts down them – this is a much more practical arrangement.
… looking somewhat ‘used’, but with plenty of fight in it yet.
… shown with the patent Cliff Prodder – very useful.
Door hinges.
On the First and Third class coach kits there is a strip of brass between a side and an end on the etch and several more short strips in the curved gap above the ends. I was rather short of space! There is an ample amount of strip for all the hinges, but using the short strips is admittedly a little fiddly. If you have obtained one of the Brake Third coach body kits I was able to fit more longer strips here which are more convenient to use. With the side held face down over a thin piece of card (to allow the hinges to appear slightly in front of, or ‘proud’ of, the surface) the strip can be poked through the rectangular holes from the back, soldered in place, cut off from the back and cleaned up. The side of the coach should be held down over the card at the top of the side where it is not curved, then the increasing distance of the curved section allows the bottom hinge to extend further through the gap – all three hinges need to be arranged along the same vertical axis (on the real coach, at least).
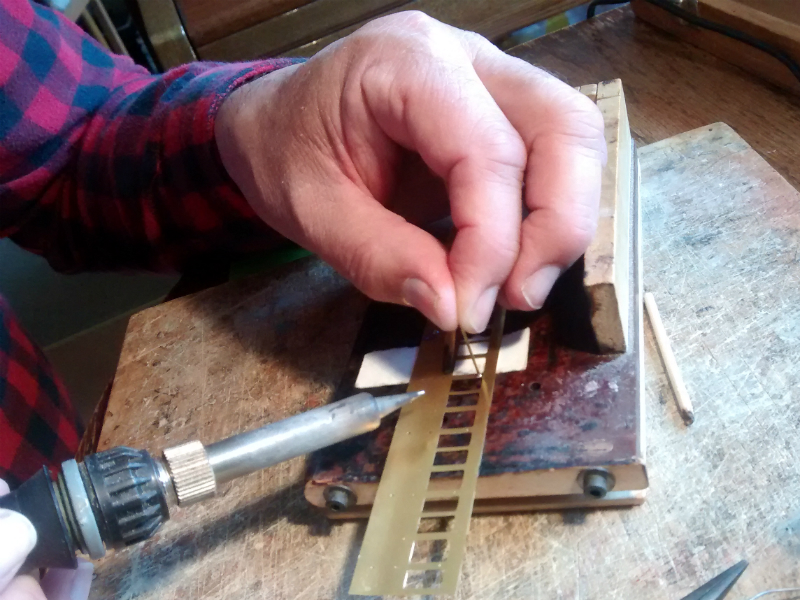
Drop-lights.
This is the stage I added these, though for some reason I took no photographs. I started the first ones by ‘tinning’ the front surface (coating with a layer of solder), but later found this was not necessary. I trapped the drop-light under the coach side, carefully adjusting its position within the door window, and then ran a seam of solder all the way around. On some of them I moved the drop-light down in the window space as if someone had opened it. If you decide to do this don’t put them down too far as they did not go all the way down. Also, they only stopped at certain positions as they were held by holes spaced two or three inches apart in a leather strap hooked over a stub on the door – visit a preserved railway if you are not familiar with the arrangement.
Door Ventilators.
I have provided representations of these on the etch for those who want an easy option, but to my eyes they are too flat if done as an etch. The Great Eastern Railway door ventilators were quite bulbous and rounded. I shall make my own in 0.375 mm or 0.5 mm thick (15 or 20 ‘thou’) Styrene, with a couple of parallel grooves scratched into a piece of strip the correct width, rounded along the top and bottom edges and cut and shaped at the ends.
Soldering sides to ends.
The first side and end clamped on the Orion Jig ready for joining together.
The side is tacked to the end with a small blob of solder at one position. Remove them from the jig at this stage to find if they are correctly aligned.
Fixed at two positions – check again. Once you are happy, run the seam all the way along.
Fitting the bottom flange.
This uses sections of the borders of the etch to provide a reinforcing flange around the base of the coach side stopping the sides from bowing in, providing fixing points and a ledge to support the chassis inside the body. Raising the flange above the bottom edge meant that when I was intending people to use the Ratio coach chassis, the base of these units would fit in the gap. With the etched chassis, you could fit the flange flush with the bottom edge and the body would then sit nicely on the chassis. Setting it up in its original intended position however means that you can fit a 1 mm thick floor in styrene (plastikard) in the gap – your choice.
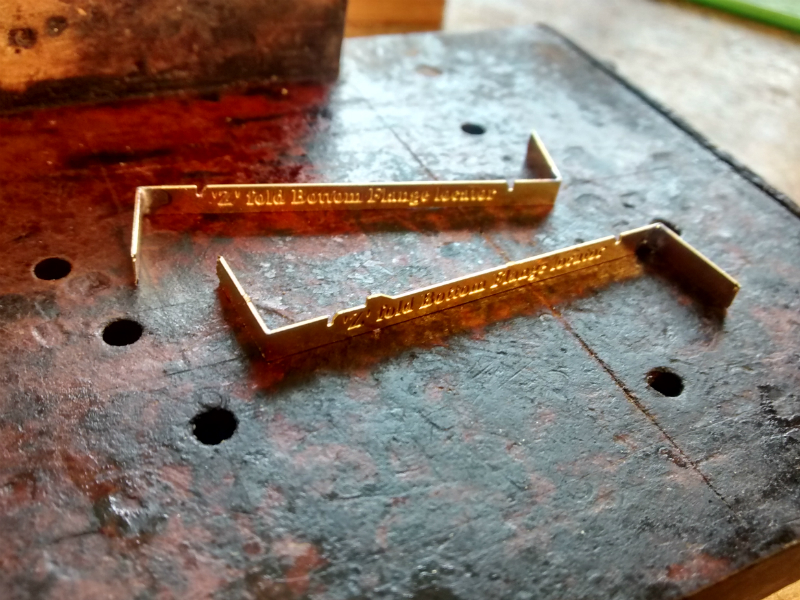
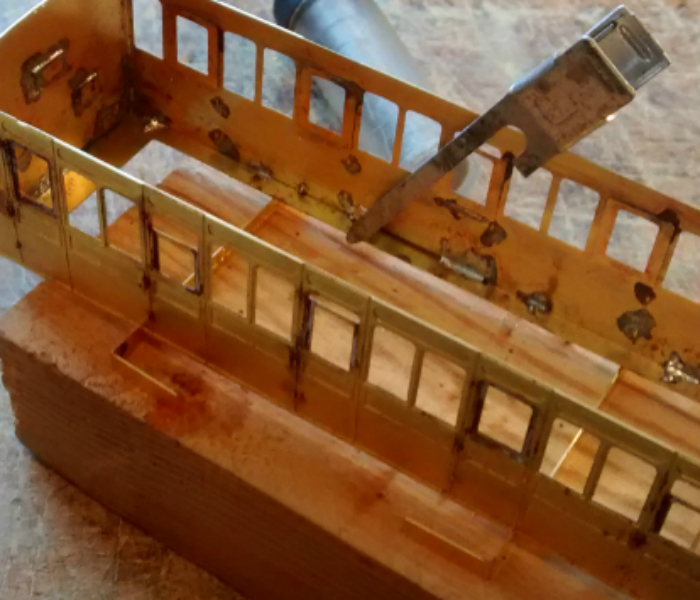
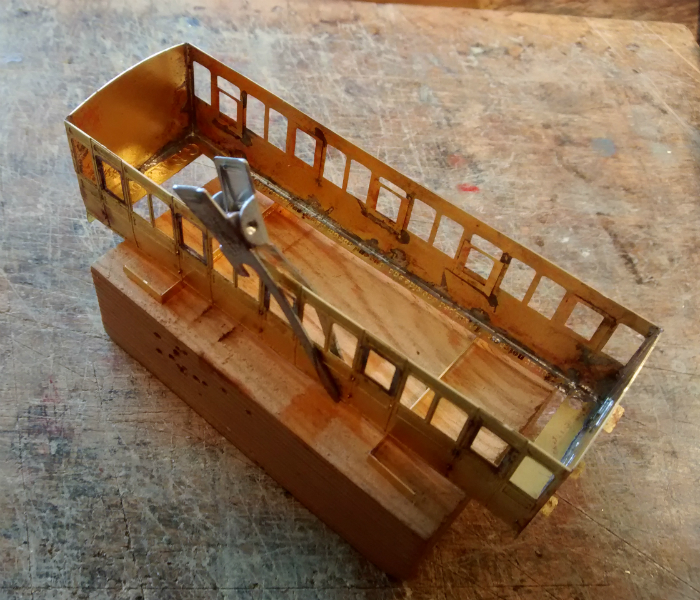
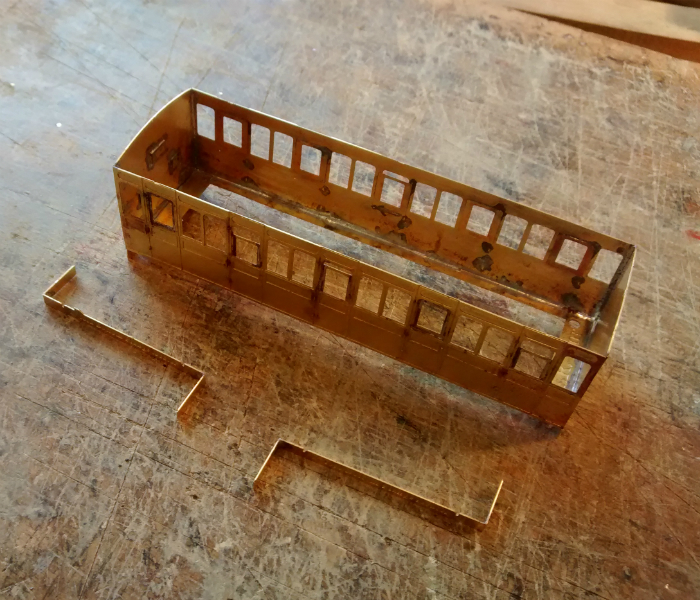
The desired final result.
It is convenient to add the end footsteps at this stage. Just bend at the fold line and push through the slots – solder in place from the back.
Duckets (lookouts) on Brake Third.
I have made these and the end of the coach as easy to fit as I can. The first stage is to fit the inner ducket ends. These provide a location for the bottom flange and also another section of the etch surround at the top each side as a top flange. These provide location for the end of the coach. On the test etch I omitted to provide slots for these to locate in and the end of the coach had to be fitted by eye – I corrected this on the production version.
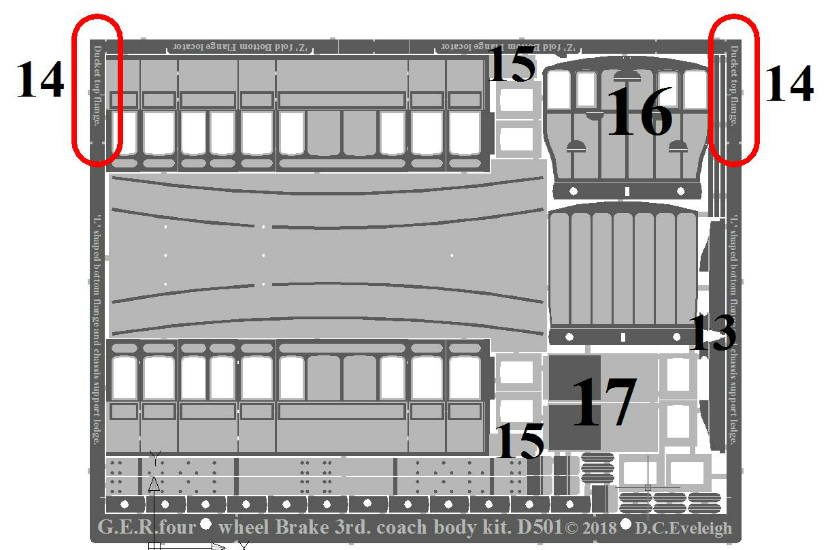
Parts identification
13 Inboard ducket ends.
14 Top flange to locate end of coach from these sections of etch border.
15 Sides extend to locate end of coach.
16 Ducket end of coach.
17 Ducket skins.
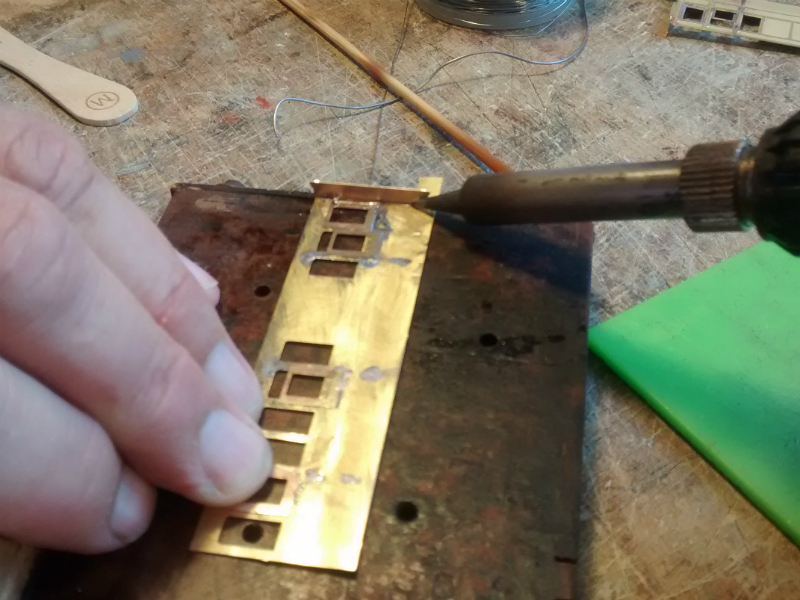
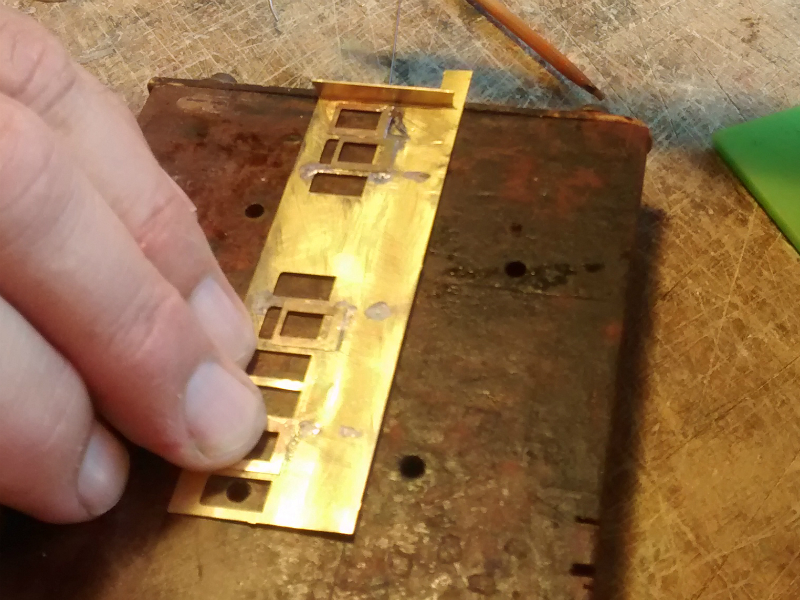
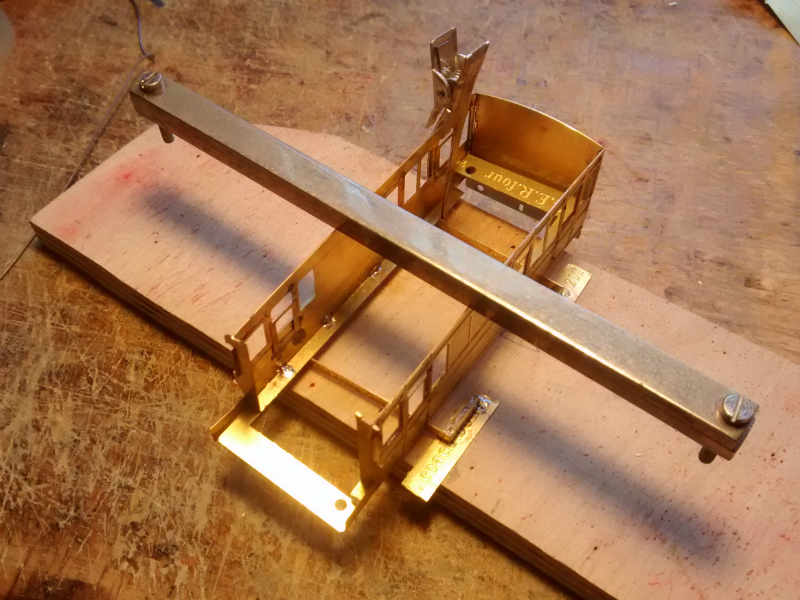
The sides ready to receive the end.
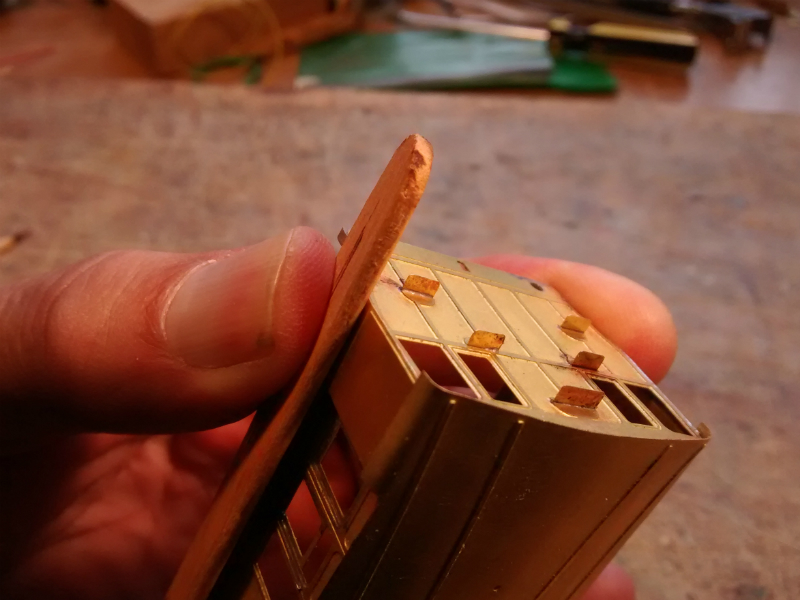
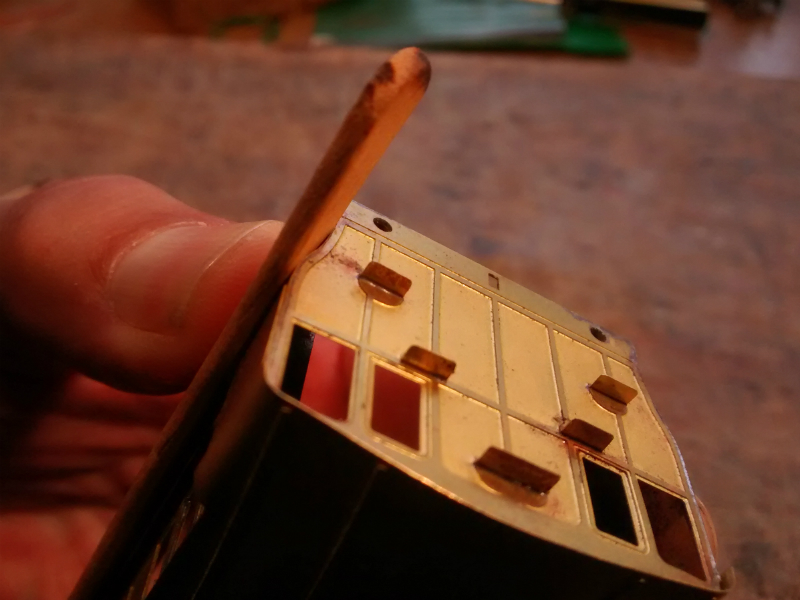
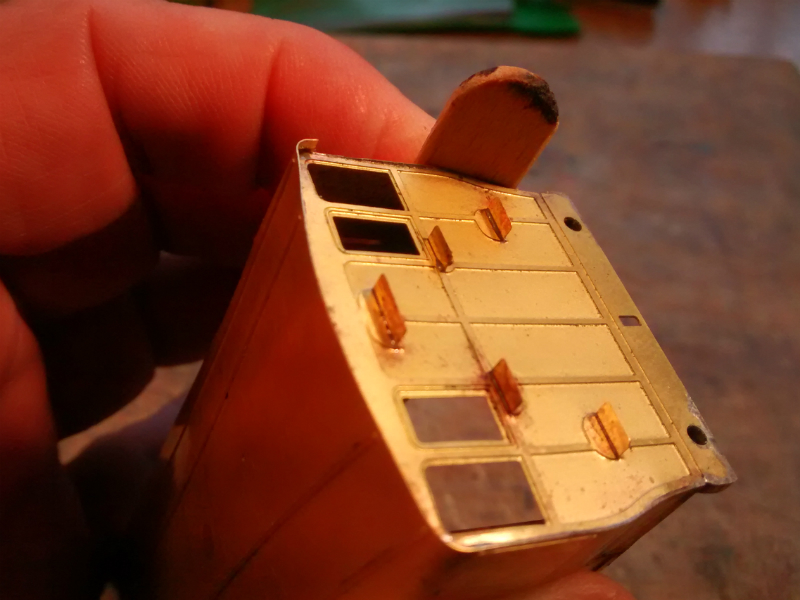
Roof
Roll to shape as for turn-unders.
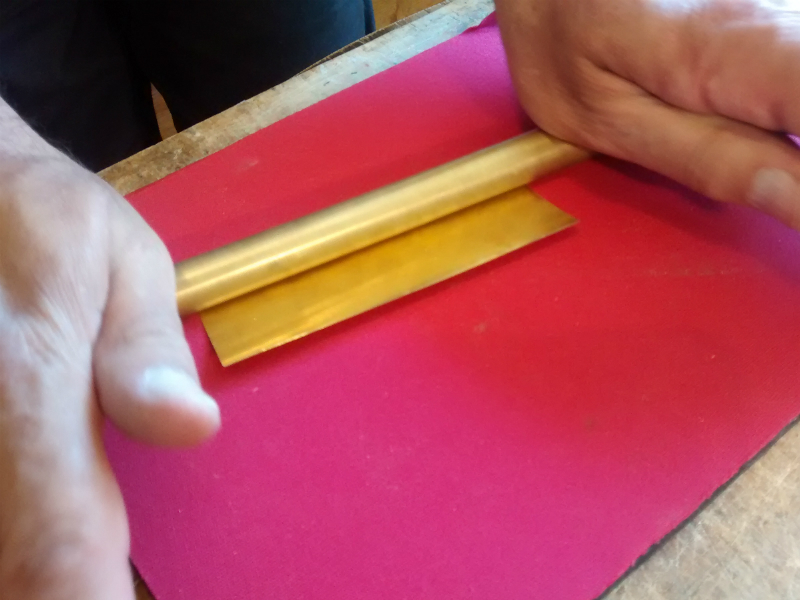
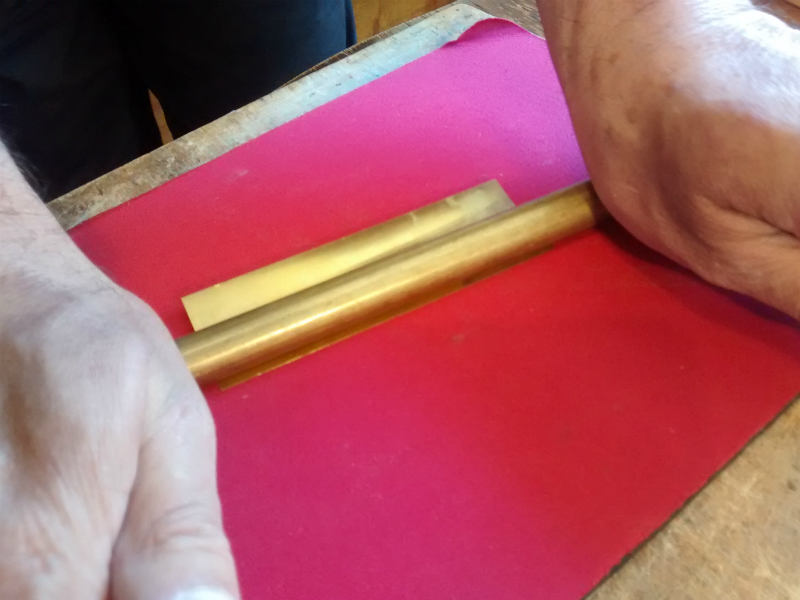
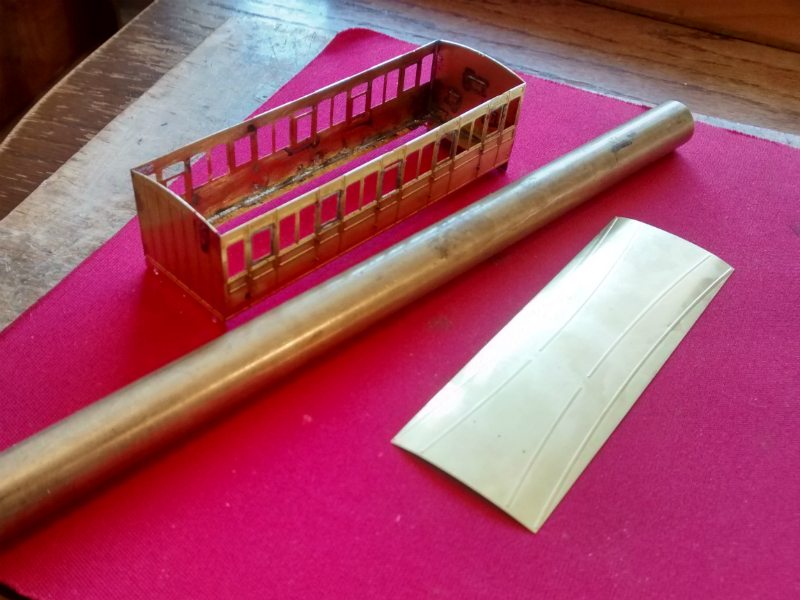
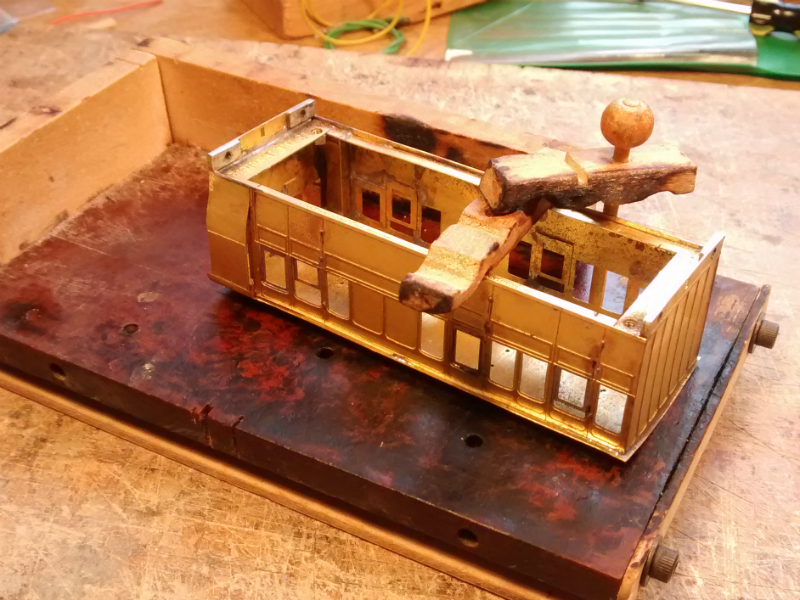
Headstock (buffer beam) end thickeners.
These are the twelve rectangles with a rounded end and a hole at the bottom of the sheet of etch. I ‘tin’ all of them one side before removing them from the etch, (put a layer of solder on having cleaned and fluxed the surface), and then stack them up in threes – one for each corner of the coach. Using my best jousting technique I put a kebab skewer end through all the holes and locate then behind the buffer hole in the headstock of the coach and solder into position. Once they are in place I add solder if necessary and use a file to profile the end gently to look like a solid baulk of wood, not four layers of etch.
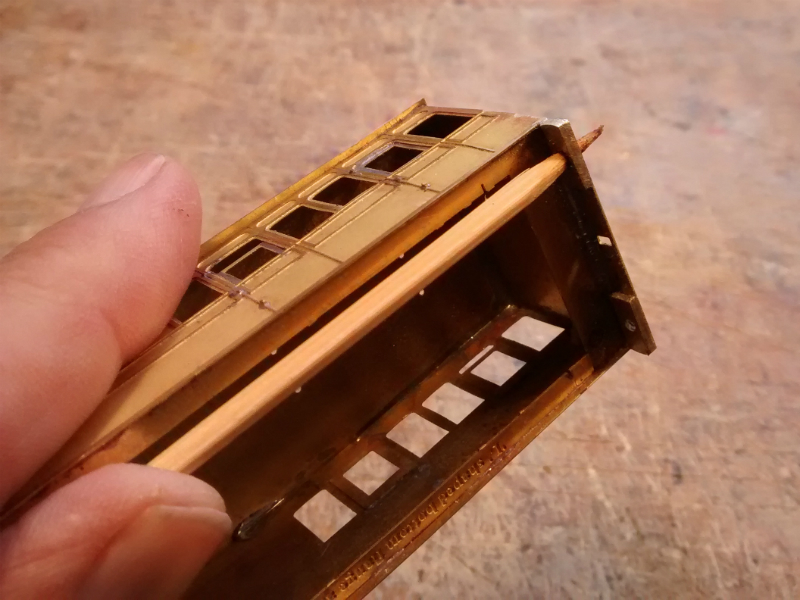
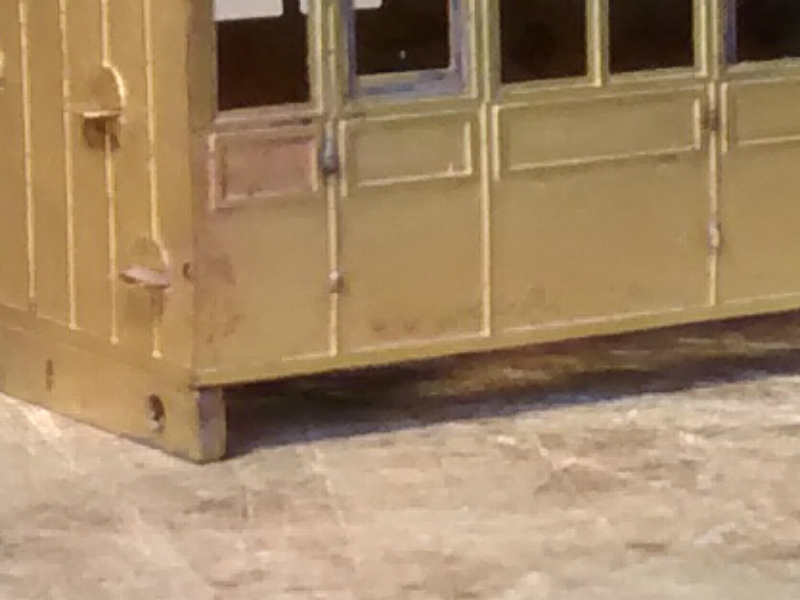
Solebar overlays.
I have provided these on the sheet if you wish to use them, but you may feel the Ratio version is satisfactory on its own.
Underframes.
There is a separate page of instructions detailing the building of the chassis, or underframes.